Tested safety of playgrounds and playground equipment
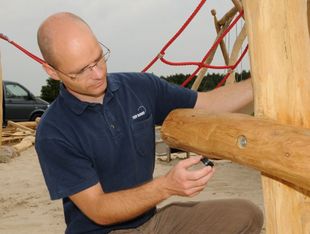
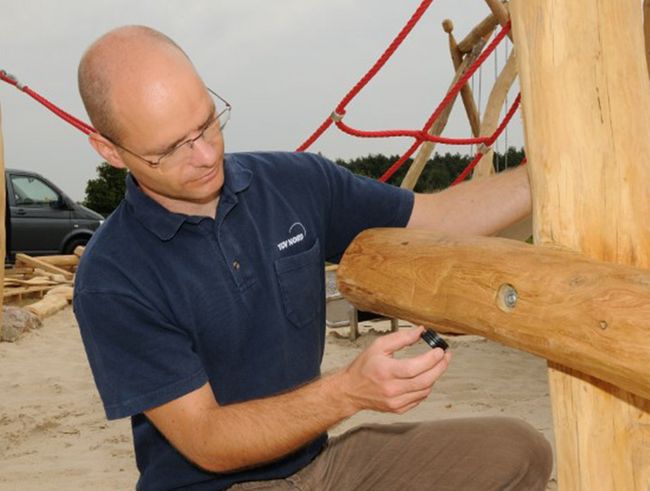
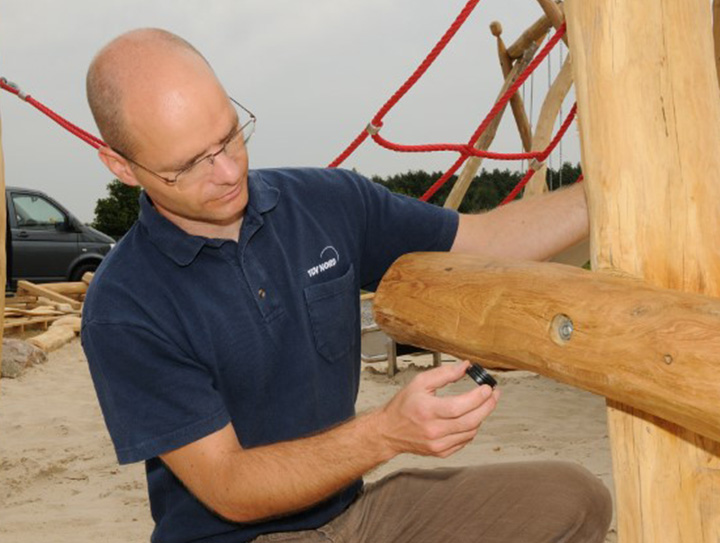
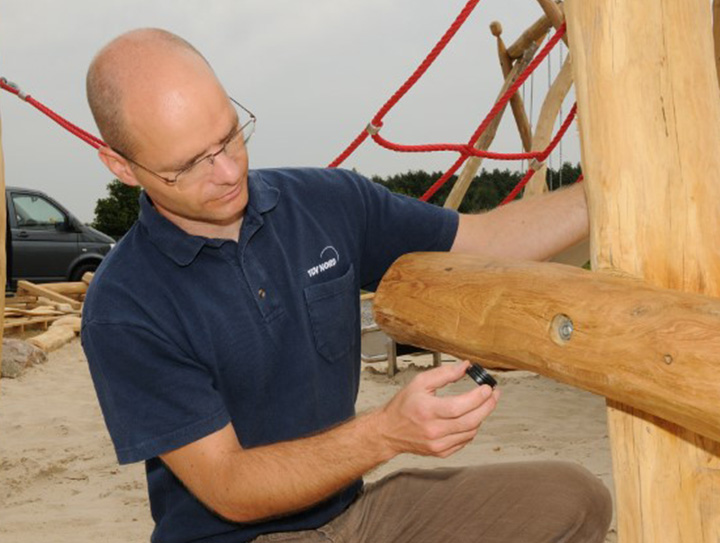
Anyone operating a playground in Germany must ensure that it is in good condition. In addition to regular inspections of playground equipment for defects or danger spots, new playground equipment must also comply with the latest standards. Playground equipment is subject to high safety requirements, which are regulated in the Product Safety Act (ProdSG). If defects are found in the playground equipment, often caused by weather conditions or even corrosion, vandalism and wear and tear, they pose a high risk of injury.
In case of an accident, the playground operator is liable. He is then obliged to prove that he has done everything necessary to ensure the safety of the children.
TÜV NORD offers the following playground inspections for this purpose:
- Annual main inspection
- Quarterly inspection
- Initial inspection of playgrounds and playground equipment
Reduction of liability risk by ensuring safety in accordance with DIN EN 1176
According to the rules and regulations of the German Social Accident Insurance (DGUV), playground operators must ensure that the safety of the playground equipment is guaranteed at all times. Thus, regular maintenance and inspection of playgrounds, play equipment and playground floors according to DIN EN 1176 is essential. The regular inspections should be executed by qualified personnel. Our experts carry out the initial inspection of playgrounds and playground equipment in schools, kindergartens and public facilities as well as performing the annual and quarterly inspections in accordance with DIN EN 1176.
Within the scope of inspections by TÜV NORD, any defects found are recorded in an inspection report by the respective playground inspector with corresponding photo documentation. The playground operator is responsible for rectifying the defectsr. This DIN EN 1176 inspection documentation serves as proof that the playground operator has fulfilled his duty to ensure safety - an important component in safety management and occupational health and safety.
Our inspection services at a glance
- Compilation of a playground/playground equipment cadastre
- Checking the boundaries to the traffic areas
- Checking the condition of the materials used
- Assessment of the individual playground equipment according to safety criteria in compliance with the requirements of accident prevention and the rules of technology such as DIN 1176, DIN EN 1177 and DIN 18034
- Photo documentation of each playground equipment and in particular of defects of playground equipment, materials, equipment and fences
- Individual report on each inspected playground with photo documentation
- Final report in printed and optionally in electronic form
- Optionally, a statistical evaluation of the inspection results and their comparison with the previous year's inspection results can be agreed upon.
- Assessment of the individual playground equipment according to safety criteria in accordance with accident prevention requirements and the rules of technology, with a focus on wear inspections of the playground equipment
- Photo documentation of each piece of playground equipment and in particular of defects on playground equipment, materials, equipment items and fences
- Individual report of a quarterly inspection of each inspected playground with photo documentation on the basis of the annual (HU) report or the previous quarterly (QU) report
- Final report of a quarterly inspection in printed and optionally in electronic form
Do you have a question?
Would you like a qoute?
Your way to the certificate
After a successful playground inspection, you will receive a certificate and a test mark in accordance with DIN EN 1176. You can use the test mark, for example, to mark the playground sign at the entrance to the playground. This makes it immediately visible that the playground equipment meets the safety requirements.
Benefit from our experience and know-how and request a quote for the inspection of your playgrounds according to DIN EN 1176 today.
Frequently asked questions DIN EN 1176
The care and maintenance of playground equipment is specified in DIN EN 1176, Part 7. The manufacturer specifies the corresponding inspection intervals for the playground equipment to the playground operator. The operator must ensure that the safety of the playground equipment is guaranteed at all times. At least once a week, a visual inspection should be carried out by the playground operator; however, shorter inspection intervals may be necessary in the case of very heavy use. Every three months, a so-called "operational inspection" must be carried out by qualified personnel. Once a year, the annual main inspection is due, e.g. by TÜV NORD, during which the condition of foundations and material is checked.
The annual main inspection and the quarterly inspection are carried out on site and include a list of all playground equipment found, the compilation of a list of defects, inspection of safety areas and boundaries to traffic areas, and photographic documentation of playground equipment (if necessary, of damage pictures). If serious defects are found on playground equipment, the playground operator is notified directly. The playground operator must then immediately block the playground equipment in question
The documentation of the playground inspection must be saved. It serves as proof, e.g. in the event of accidents, that the playground operator has fulfilled his duty to ensure road safety. On the other hand, the documentation ensures a check on whether the identified defects have actually been eliminated. In addition, the photo documentation made during the inspections provides valuable support in identifying the defects found and in their subsequent elimination. It is thus a highly simplifying instrument in the safety management of the playgrounds.
- Inspection and verification by an independent, neutral inspection body
- Fulfilment of the obligation to ensure road safety
- Legally compliant documentation of playground inspection
- Upon successful inspection: right to use the test mark "Annual playground inspection" in accordance with DIN EN 1176
The annual main inspection of playgrounds basically includes the determination of the general operationally safe condition of facilities, foundations and surfaces by an expert. It also serves as proof that the operator has fulfilled his obligation to ensure road safety. The operationally safe condition can be impaired, for example, by the effects of weather (rotting and corrosion), changes in safety of the installation (repairs carried out or additionally installed or replaced parts of the installation), but also by vandalism. Depending on the equipment, this may also make it necessary to excavate or expose certain parts of the playground equipment. Our scope of services includes the following inspections:
- Construction
- Stability
- Dimensions
- Connecting elements
- Bearing
- Free fall height
- Safety distances
- Handrails
- Stairways
- Balustrades
- Degrees of wear
- Fall protection
- Roof surfaces
- Crushing and shearing points
- Catch points for the head, body of swinging masses
- Ropes
- Rope attachments
- Handholds
- Seats
- Sliding surfaces
- Seating areas
After a successful inspection, a certificate is issued stating that the inspection has been carried out in accordance with the current legal requirements. In addition, an inspection badge is awarded. This badge can be used to mark the regular inspection on the playground sign located at the entrance.
The quarterly inspections build on the test results of the previous annual main inspection. The test reports of the quarterly inspections thus also include the elimination of defects in playground equipment identified during the main inspection. If, for example, advanced rotting of wooden components of the equipment structure was detected during the previous inspection without the equipment having to be immediately blocked, the progress of the rotting is also checked during the quarterly inspections and, if necessary, information is provided on the immediate blocking of the play equipment.
The operator of a playground facility must do everything to avert potential dangers, as he or she is responsible for ensuring the safety of the entire playground facility. This also includes dangers that may arise, for example, from damage to the playground equipment. Regular inspection and maintenance, as provided by the manufacturers of the playground equipment, in coordination with the cycle of DIN EN 1176, reduces the liability risk for playground operators.
Focus topic DIN EN 1177: Testing fall protection and shock absorption
Playground operators are required to determine the shock absorption of playground floors and the critical fall height at the playground with the help of DIN EN 1177. The term "critical fall height" refers to the maximum height up to which the playground floor still provides sufficient shock absorption if, for example, a child falls from the swing onto the ground. Depending on the floor material used, the maximum fall height is already 0.60m.
In order to check whether the shock absorption of playground floors is sufficient, various key figures must be taken into account. The same applies to the critical fall height and the selection of floor materials. Besides fall protection slabs, operators also use loose materials such as sand, gravel or wood or wood chips for fall protection of their playground. Here, other requirements apply to the test procedure
TÜV NORD supports you as a competent partner in testing of your playgrounds according to the DIN EN 1177 standard.
Frequently asked questions DIN EN 1177
In order for the floor of a playground to provide sufficient impact protection, the operators must observe the following key figures, among others:
- Playground equipment requires at least 1.50 m of obstacle-free space around it, measured from the respective outermost parts of the equipment
- from a drop height of 1,50 m, the impact area is extended according to this fromula:
Lenght of impact area (m) = (of free fall height) + 0,5 m
- for equipment with a drop height lower than 0.60 m and equipment that causes movement (e.g. swings, merry-go-rounds, slides, cable cars), shock-absorbing floors are required under the entire impact area
DIN EN 1177 regulates the testing of shock-absorbing playground floors. However, basic safety requirements for the floors are defined in Part 1 of DIN EN 1177. It specifies, for instance, which flooring materials operators are allowed to use for their playgrounds in order to meet the requirements for fall protection and shock absorption.
Which floor materials are permissible according to DIN EN 1177?
- Concrete or stone
- Bitumen-bonded soils
- Topsoil
- Turf
- Bark mulch
- Wood chips
- Sand
- Gravel
Certification with TÜV NORD
TÜV NORD is your reliable internationally recognized partner for testing and certification services. Our experts and auditors have in-depth knowledge and support you in the certification process with objective feedback. We guarantee independence and neutrality as well as continuity of support - worldwide: Thanks to our global network, we can offer you our testing and certification services across borders.